Frequently asked questions from customers
- What does "Select Mode" and "Reset" do?
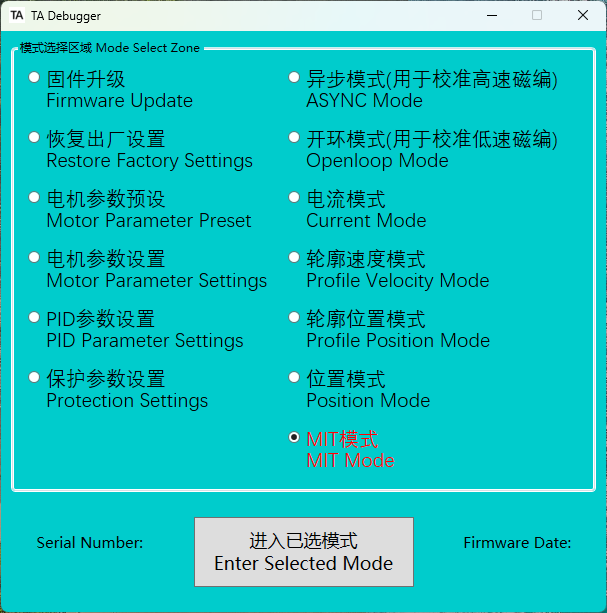
Select XX mode |
|
|
|
|
|
|
|
|
|
- There are 13 modes in the above picture, all of which are entered through the above messages. Among them, asynchronous, open loop, firmware upgrade, and protection parameter setting are generally not used. The function on the left side of the picture is the parameter setting function. If you need to modify the configuration parameters, it is recommended to operate in the host computer software. The configuration content here is all in frash. If you modify the pid value, acceleration and deceleration value, etc. in real time, the content it modifies is in RAM.
- The modes on the right side of the picture are all operating modes. Entering a mode is equivalent to enabling the actuator. The actuator will not rotate or output torque if it does not enter any mode.
- Exit mode (reset) is equivalent to canceling the actuator, and the contents in the RAM will be restored, including the real-time set PID and acceleration and deceleration values, and the position value of the motor side.
Exiting a mode is not a way to stop the actuator. The only way to stop the actuator is to send a command to stop it within the mode.
-
How to obtain the status of the actuator When the actuator enters the current, contour speed, contour position, position, or MIT modes, there are three bytes in the message that can set the automatic feedback cycle (ms) of the three feedback messages respectively. If the cycle is set to 0, the corresponding feedback message will not be fed back. These three messages basically contain all the states of the actuator required by the user. After exiting the mode (reset), there will be no feedback.
-
Modification of zero offset, current limit, speed limit, position limit or other configuration parameters These configurations generally need to be set in the host computer software, and can be changed directly by entering the "Motor Parameter Setting" mode. Although it is possible to send messages directly for configuration, it is not recommended.