TA-Debugger
Host computer debugging software, used to set parameters or drive actuators
Click to download the latest version:
Changelog:
Date: July 25, 2025 Version: 20250724
- The brake uses a 95% duty cycle when the power is off, so that the capacitance required to close the brake when the power is off is as small as possible.
Date: July 21, 2025 Version: 20250714
- The Chinese name of MIT mode is changed to hybrid mode
- Motor parameter preset mode Here, the configuration of NTC resistor is added to support the situation that some individual motor materials are not in accordance with the agreed 10K+3380
- The warning message for adjusting the positive direction of the motor rotation on the original page has been changed to be triggered after clicking the SET button
- Changes in MCU software:
- Previously, if the motor speed exceeded 7000rpm, the speed waveform would be abnormal. This update fixes this problem.
- Previously, when not entering any mode, sending the command to operate the brake would cause an exception. This update handles this problem. However, there is a small difference. For example, after entering any mode, sending 1500 means 15V voltage. When not entering any mode, sending 1500 means the duty value is 1500 and the full value is 4000. If the power supply voltage is 24V, 1500 only means 9V=1500/4000*24. The reason for this difference is that in the idle state without entering any mode, the timer and ADC are not working, so the power supply voltage cannot be collected.
- In addition, the operating range of the PWM duty cycle of the brake is opened to 3800/4000, which is 95%.
📌
note:
After updating the firmware, you can choose not to restore the factory settings, or you can choose to restore the factory settings. If you do not want to restore the factory settings, you need to manually fill in the motor NTC parameters on the motor parameter preset page. If you restore the factory settings, no additional operations are required.
Date: April 30, 2025 Version: 20250430
Fixed the bug of brake locking or unlocking
📌
After this version is updated, it can be used directly without restoring factory settings
Date: March 28, 2025 Version: 20250325
Update firmware and debug software:
- The input value limits of each motion control mode can be set in the ini file. And some interactive bugs have been solved
- About the brake:
- Added brake automatic opening(closing) voltage setting to the parameter preset page of the debugging software
- The program internally processes the brake, and the original PWM duty cycle method is updated to recalculate the PWM corresponding to the accurate voltage value according to the current power supply voltage, and then apply it to the brake. This prevents the brake from being too impacted by a high voltage power supply such as 50V, causing rebound.
- On the motion control page, the brake input PWM is changed to a voltage with a unit of 0.01V, and the value range remains roughly the same. For example, if you enter 2000, the original meaning is 2000 PWM, 2000/4000=50%, which is a 50% duty cycle. The new meaning is 20.00V, which is 20V. For another example, if you enter 1500, it is 15V
- About temperature:
- On the protection setting page of the debugging software, relax the maximum value of over-temperature protection to 180
- The temperature display range of the motion control page of the debugging software is adjusted from -128~+127℃ to -75~+180℃. This change is made for the convenience of extreme testing.
- When the motor NTC is not connected, that is, when the NTC resistor is infinite, the temperature is displayed as around -65℃. This is a bug, this should have been the case, but the conversion process had an unexpected result that caused the negative temperature to become 0. This update fixes this bug.
- Change the description of the MIT parameter in the “pid parameter setting” of the debugging software
📌
Note:
- If the motor is already on the arm and it is not convenient to recalibrate it, you need to manually go to the parameter preset page of the debugging software and set the voltage value of the automatic opening(closing) of the brake to 1500, so that it can work normally later.
- For the free actuator, simply restore the factory settings and recalibrate it.
Date: March 25, 2025 Version: 20250323
Update debugging software:
- Some sorting and supplementation of the debugging software motion control page, adding English comparison
- Waveform drawing, configurable number of points for refreshing the page

- CAN Feedback 3 cycle parameters, configurable return time
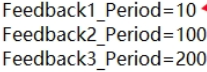
Date: March 19, 2025 Version: 20250319
- The MIT mode operation cycle is changed from 10ms to 2ms, that is, 500Hz
- In order to facilitate the installation of different reducers on the same motor, the position PID and MIT PID are now based on the motor end encoder.
- The position P parameter is 100 times smaller than before, and the MIT P parameter is 100 times smaller than before.
- If you change the reduction ratio from 101 to 81/51/31 in the future, you can directly modify the reduction ratio on the parameter setting page. No other changes are required.
- The debugging software modifies the MIT page initialization P value from 9 to 0.09
📌
Note:
- For motors that are already on the arm or motors that are not convenient to restore to factory settings and recalibrate, you need to manually change the position default P parameter from 0.8 to 0.008. The MIT P parameter is changed from 9 to 0.09
- For motors that can rotate freely, just restore to factory settings and recalibrate.